Introduction to Mechatronic Design, 1st edition
Published by Pearson (December 21, 2010) © 2011
- J Edward Carryer
- Hardcover, paperback or looseleaf edition
- Affordable rental option for select titles
- Free shipping on looseleafs and traditional textbooks
For upper level and graduate Mechatronics courses in Electrical, Computing, or Mechanical & Aerospace Engineering.
¿
Unlike other texts on mechatronics that focus on derivations and calculations, Introduction to Mechatronic Design, 1e, takes a narrative approach, emphasizing the importance of building intuition and understanding before diving into the math. The authors believe that integration is the core of mechatronics—and students must have a command of each of the domains to create the balance necessary for successful mechatronic design—and devote sections of the book to each area, including mechanical, electrical, and software disciplines, as well as a section on system design and engineering. A robust package of teaching and learning resources accompanies the book.
A focus on developing intuition. The authors believe that developing intuition enables students to move from problem statements to problem solutions and, as a result, create new designs. This approach is taken throughout the book.
Ex: In Chapter 9, Basic Circuit Elements, the material is presented with a running fluid flow analogy to help develop intuition about the behavior of basic circuit elements.
Practical application information. The book helps students develop the ability to understand a data sheet for devices they have not seen or used before.
Ex: See Chapter 16, Digital Inputs and Outputs and Chapter 17, Digital Outputs and Power Drivers.
Balanced coverage. Unlike other textbooks on the subject, this text provides substantial coverage of each engineering domain. In addition, while other books focus on control systems engineering, Carryer/Kenny/Ohline treat the topic as a separate issue and cover it at an appropriate level for a mechatronics text.
Software design. While software design is often omitted from other texts, most of the software section of this text is devoted to software design (as opposed to the mechanics of any particular software language or microcontroller architecture). The authors believe that software should be designed and carefully planned, and provide structures which serve to help organize the design of software specific to embedded systems.
Ex: See Chapter 5, Programming Structures for Embedded Systems.
A section devoted to Systems Design. System design as a topic is also missing from most other texts. The authors devote a section of the book to the topic, including chapters covering rapid prototyping, troubleshooting, project planning and management, and finally a case study that shows how two student projects unfolded, and highlights the process of integration, and the alternatives and design decisions that were made along the way.
Emphasis on integration. Integration can be both a blessing and a curse in mechatronics. The authors believe that the best mechatronic solutions take full advantage of the flexibility and opportunities that result from combining the disciplines. However, since those new to the subject tend to underestimate the difficulty of integration, the authors offer tools and guidance to lead the student through the material successfully.
Ex: See Chapter 32, Mechatronic Synthesis.
Collateral materials. This text is fully supported by a package of robust resources, for both instructors and students, containing well thought-out and vigorously tested (for over 15 years) lab assignments, hardware, and software.
An instructor community Wiki that is monitored by the authors, provides a continually growing set of resources. This medium allows instructors to share experiences, ask for advice and receive feedback from both the authors and the instructor community. Instructors can preview the site at http://www.pearsonhighered.com/carryer. Select "View the Community Wiki" and log in using a user name of wikiuser0001 with a password of bear3lemon.
Part 1: Introduction
Preface
Chapter 1 Introduction
1.1 Philosophy
1.3 Who Should Study Mechatronics?
1.3 How to Use this Book
1.4 Summary
Part 2: Software
Chapter 2 What’s a Micro?
2.1 Introduction
2.2 What IS a “Micro”?
2.3 Microprocessors, Microcontrollers, Digital Signal Processors (DSP’s) and More
2.4 Microcontroller Architecture
2.5 The Central Processing Unit (CPU)
2.5.1 Representing Numbers in the Digital Domain
2.5.2 The Arithmetic Logic Unit (ALU)
2.6 The Data Bus and the Address Bus
2.7 Memory
2.8 Subsystems and Peripherals
2.9 Von Neumann Architecture
2.10 The Harvard Architecture
2.11 Real World Examples
2.11.1 The Freescale MC9S12C32 Microcontroller
2.11.2 The Microchip PIC12F609 Microcontroller
2.12 Where to Find More Information
2.13 Homework Problems
Chapter 3 Microcontroller Math and Number Manipulation
3.1 Introduction
3.2 Number Bases and Counting
3.3 Representing Negative Numbers
3.4 Data Types
3.5 Sizes of Common Data Types
3.6 Arithmetic on Fixed Size Variables
3.7 Modulo Arithmetic
3.8 Math Shortcuts
3.8 Boolean Algebra
3.9 Manipulating Individual Bits
3.10 Testing Individual Bits
3.11 Homework Problems
Chapter 4: Programming Languages
4.1 Introduction
4.2 Machine Language
4.3 Assembly Language
4.4 High-Level Languages
4.5 Interpreters
4.6 Compilers
4.7 Hybrid Compiler/Interpreters
4.8 Integrated Development Environments (IDEs)
4.9 Choosing a Programming Language
4.10 Homework Problems
Chapter 5: Program Structures for Embedded Systems
5.1 Background
5.2 Event Driven Programming
5.3 Event Checkers
5.4 Services
5.5 Building an Event Driven Program
5.6 An Example
5.7 Summary of Event Driven Programming
5.8 State Machines
5.9 A State Machine in Software
5.10 The Cockroach Example as a State Machine
5.11 Summary
Homework Problems
Chapter 6 Software Design
6.1 Introduction
6.2 Building as a Metaphor for Creating Software
6.3 Introducing Some Software Design Techniques
6.3.1 Decomposition
6.3.2 Abstraction and Information Hiding
6.3.3 Pseudo-Code
6.4 Software Design Process
6.4.1 Generating Requirements
6.4.2 Defining the Program Architecture
6.4.3 The Performance Specification
6.4.4 The Interface Specification
6.4.5 Detail Design
6.4.6 Implementation
6.4.6.1 Intra-Module Organization
6.4.6.2 Writing the Code
6.4.7 Unit Testing
6.4.8 Integration
6.5 The Sample Problem
6.5.1 Requirements for the Morse Code Receiver
6.5.2 The Morse Code Receiver System Architecture
6.5.3 The Morse Code Receiver Software Architecture
6.5.4 The Morse Code Receiver Performance Specifications
6.5.5 The Morse Code Receiver Interface Specification
6.5.5.1 The Button Module Interface Specification
6.5.5.2 The Morse Elements Module Interface Specification
6.5.5.3 The Morse Decode Module Interface Specification
6.5.5.4 The LCD Display Module Interface Specification
6.5.6 The Morse Code Receiver Detail Design
6.5.6.1 Button Module Detail Design
6.5.6.2 Morse Elements Detail Design
6.5.6.3 Morse Decode Detail Design
6.5.6.4 Display Detail Design
6.5.6.5 Main Detail Design
6.5.7 The Morse Code Receiver Implementation
6.5.8 The Morse Code Receiver Unit Testing. 6-28
6.5.9 The Morse Code Receiver Integration
6.6 Homework Problems
Chapter 7 Communications
7.1: Introduction
7.2: Without a Medium, there is no Message
7.3: Bit-Parallel and Bit-Serial Communications
7.3.1: Bit-Serial Communications
7.3.1.1: Synchronous Serial Communications
7.3.1.2: Asynchronous Serial Communications
7.3.2: Bit Parallel Communications
7.4: Signaling Levels
7.4.1: TTL/CMOS Levels
7.4.2: RS-232
7.4.3: RS-485
7.5: Communicating Over Limited Bandwidth Channels
7.5.1: Telephones and Modems
7.5.1.1: Modulation Techniques
7.5.1.2: Amplitude Modulation (AM)
7.5.1.3: Frequency Modulation (FM)
7.5.1.4: Phase Modulation (PM)
7.5.1.5: Quadrature Amplitude Modulation (QAM)
7.6: Communicating with Light
7.7: Communicating over a Radio
7.7.1: RF Remote Controls
7.7.2: RF Data Links
7.7.3: RF Networks
7.8: Homework Problems
Chapter 8 : Microcontroller Peripherals
8.1 : Accessing the Control Registers
8.2 : The Parallel Input/Output Subsystem
8.2.1 : The Data Direction Register
8.2.2 : The Input/Output Register(s)
8.2.3 : Shared Function Pins
8.3 : Timer Subsystems
8.3.1 : Timer Basics
8.3.2 : Timer Overflow
8.3.3 : Output Compare
8.3.4 : Input Capture
8.3.5 : Combining Input Capture and Output Compare to Control an Engine
8.4 : Pulse Width Modulation (PWM)
8.5 : PWM Using the Output Compare System
8.6 : The Analog-to-Digital (A/D) Converter Subsystem
8.6.1 : The Process for Converting an Analog Input to a Digital Value
8.6.2 : The A/D Converter Clock
8.6.3 : Multiplexer Switching Transients and DC Effects
8.6.4 : Automating the A/D Conversion Process
8.7 : Homework Problems
Part 3: Electronics
Chapter 9 Basic Circuit Analysis and Passive Components
9.1 Voltage, Current and Power
9.2 Circuits and Ground
9.3 Laying Down the Laws
9.4 Resistance
9.4.1 Resistors in Series and Parallel
9.4.2 The Voltage Divider
9.5 Thevenin Equivalents
9.6 Capacitors
9.6.1 Capacitors in Series and Parallel
9.6.2 Capacitors and Time-Varying Signals
9.7 Inductors
9.7.1 Inductors and Time-Varying Signals
9.8 The Time and Frequency Domains
9.9 Circuit Analysis with Multiple Component Types
9.9.1 Basic RC Circuit Configurations
9.9.2 Low-Pass RC Filter Behavior in the Time Domain
9.9.3 High-Pass RC Filter Behavior in the Time Domain
9.9.4 RL Circuit Behavior in the Time Domain
9.9.5 Low-Pass RC Filter Behavior in the Frequency Domain
9.9.6 High-Pass RC Filter Behavior in the Frequency Domain
9.9.7 High-Pass RC Filter with a DC Bias
9.10 Simulation Tools
9.10.1 Limitations of Simulation Tools
9.11 Real Voltage Sources
9.12 Real Measurements
9.12.1 Measuring Voltage
9.12.2 Measuring Current
9.13 Real Resistors
9.13.1 A Model for a Real Resistor
9.13.2 Resistor Construction Basics
9.13.3 Carbon Film Resistors
9.13.4 Metal Film Resistors
9.13.5 Power Dissipation in Resistors
9.13.6 Potentiometers
9.13.7 Multi-Resistor Packages
9.13.8 Choosing Resistors
9.14 Real Capacitors
9.14.1 A Model for a Real Capacitor
9.14.2 Capacitor Construction Basics
9.14.3 Polar vs. Non-Polar Capacitors
9.14.4 Ceramic Disk Capacitors
9.14.5 Monolithic Ceramic Capacitors
9.14.6 Aluminum Electrolytic Capacitors
9.14.7 Tantalum Capacitors
9.14.8 Film Capacitors
9.14.9 Electric Double Layer Capacitors / Super capacitors
9.14.10 Capacitor Labeling
9.14.10.1 Ceramic Capacitor (Disc and MLC) Labeling
9.14.10.2 Aluminum Electrolytic Capacitor Labeling
9.14.10.3 Tantalum Capacitor Labeling
9.14.10.4 Film Capacitor Labeling
9.14.11 Choosing a Capacitor
9.15 Homework Problems
Chapter 10 Semiconductors
10.1 Doping, Holes and Electrons
10.2 Diodes
10.2.1 The VI Characteristic for Diodes
10.2.2 The Magnitude of Vf
10.2.3 Reverse Recovery
10.2.4 Schottky Diodes
10.2.5 Zener Diodes
10.2.6 Light Emitting Diodes
10.2.7 Photo-Diodes
10.3 Bipolar Junction Transistors
10.3.1 The Darlington Pair
10.3.2 The Photo-Transistor
10.4 MOSFETs
10.5 hoosing Between BJTs and MOSFETs
10.5.1 When Will a BJT be the Best (or Only) Choice?
10.5.2 When Will a MOSFET be the Best (or Only) Choice?
10.5.3 How Do You Choose When Either a MOSFET or a BJT Could Work?
10.6 Multi-Transistor Circuits
10.7 Reading Transistor Data Sheets
10.7.1 Reading a BJT Data Sheet
10.7.2 Reading a MOSFET Data Sheet
10.7.3 A Sample Application
10.7.4 A Potpourri of Transistor Circuits
10.8 Homework Problems
Chapter 11 : Operational Amplifiers
11.1 : Operational Amplifier Behavior
11.2 : Negative Feedback
11.3 : The Ideal Op-Amp
11.4 : Analyzing Op-Amp Circuits
11.4.1 : The Golden Rules
11.4.2 : The Non-Inverting Op-Amp Configuration
11.4.3 : The Inverting Op-Amp Configuration
11.4.3.1 : The Virtual Ground
11.4.3.2 : There is Nothing Magic About Ground
11.4.4 : The Unity Gain Buffer
11.4.5 : The Difference Amplifier Configuration
11.4.6 : The Summer Configuration
11.4.7 : The Trans-Resistive Configuration
11.4.8 : Computation with Op-Amps
11.5 : The Comparator
11.5.1 : Comparator Circuits
11.6 : Homework Problems
Chapter 12 : Real Operational Amplifiers and Comparators
12.1 : Real Op-Amp Characteristics — How the Ideal Assumptions Fail
12.1.1 : Non-Infinite Gain
12.1.2 : Variation in Open Loop Gain with Frequency
12.1.3 : Input Current is Not Zero
12.1.3.1 : Input Bias Current and Input Offset Current
12.1.3.2 : Input Impedance
12.1.4 : The Output Voltage Source is Not Ideal
12.1.5 : Other Non-Idealities
12.1.5.1 : Input Offset Voltage
12.1.5.2 : Power Supplies
12.1.5.3 : Input Common Mode Voltage Range
12.1.5.5 : Input Common Mode Rejection Ratio
12.1.5.6 : Temperature Effects
12.2 : Reading an Op-Amp Data Sheet
12.2.1 : Maxima, Minima and Typical Values
12.2.2 : The Front Page
12.2.3 : The Absolute Maximum Ratings Section
12.2.4 : The Electrical Characteristics Section
12.2.5 : The Packaging Section
12.2.6 : The Typical Applications Section
12.3 : Reading a Comparator Data Sheet
12.3.1 : Comparator Packaging
12.4 : Comparing Op-Amps
12.5 : Homework Problems
Chapter 13 Sensors
13.1 Introduction
13.2 Sensor Output & Microcontroller Inputs
13.3 Sensor Design
13.3.1 Measuring Temperature with a Thermistor
13.3.2 Measuring Acceleration
13.3.3 Definitions of Sensor Performance Characteristics
13.4 Fundamental Sensors and Interface Circuits
13.4.1 Switches as Sensors
13.4.2 Interfacing to Switches
13.4.3 Resistive Sensors
13.4.4 Interfacing to Resistive Sensors
13.4.4.1 Using a Resistive Sensor in a Voltage Divider
13.4.4.2 Measuring Resistance Using a Current Source
13.4.4.3 The Constant Current Circuit
13.4.4.4 The Wheatstone Bridge
13.4.5 Capacitive Sensors
13.4.6 Interfacing to Capacitive Sensors
13.4.6.1 Measuring Capacitance with a Step Input
13.4.6.2 Measuring Capacitance with an Oscillator
13.4.6.3 Measuring Capacitance with a Wheatstone Bridge
13.5 A Survey of Sensors
13.5.1 Light Sensors
13.5.1.1 Photodiodes
13.5.1.2 Phototransistors
13.5.1.3 Emitter-Detector Pair Modules
13.5.1.4 Photocells
13.5.2 Strain Sensors
13.5.2.1 Metal Foil Strain Gages
13.5.2.2 Piezoresistive Strain Gages
13.5.2.3 Load Cells
13.5.3 Temperature Sensors
13.5.3.1 Thermocouples
13.5.3.2 Thermistors
13.5.4 Magnetic Field Sensors
13.5.4.1 Hall Effect Sensors
13.5.4.3 Reed Switches
13.5.5 Proximity Sensors
13.5.5.1 Capacitive Proximity Sensors
13.5.5.2 Inductive Proximity Sensors
13.5.5.3 Ultrasonic Proximity Sensors
13.5.6 Position Sensors
13.5.6.1 Potentiometers
13.5.6.2 Optical Encoders
13.5.6.3 Inductive Pickups / Gear Tooth Sensors
13.5.6.4 Reflective Infrared Sensors
13.5.6.5 Capacitive Displacement Sensors
13.5.6.6 Ultrasonic Displacement Sensors
13.5.6.7 Flex Sensors
13.5.7 Acceleration Sensors
Ed Carryer is the Director of the Smart Product Design Laboratory (SPDL) in the Design Division of Mechanical Engineering at Stanford University. He is¿ currently a Consulting Professor in the Design Division of Mechanical Engineering. He received his Ph.D. degree in Mechanical Engineering from Stanford University in 1992. Prior to that, he received an M.S. in Bio-Medical Engineering from the University of Wisconsin, Madison in 1978. His B.S.E. was awarded from the Illinois Institute of Technology in 1975, where he was a member (1/3) of the first graduating class of the Education and Experience in Engineering (E 3)program.
Dr. Carryer's industrial experience varies wildly, from designing water treatment facilities for coal and nuclear power plants for Sargent & Lundy to designing the electronic controller for an Arctic Heated Glove under contract to NASA. He spent eight years in the Detroit area working in and about the auto industry. During that time he worked for Ford, GM and AMC on electronic engine control systems, predominantly for turbo-charged engines. He has an active design consultancy that has tackled such varied projects as an engine controller for an outboard motor manufacturer, an automated blood gas analyzer, and a turbo-charger boost control system for a new type of turbo-charger.
Matt Ohline is an Associate Consulting Professor in the Design Division of Mechanical Engineering at Stanford University.
Thomas Kenny is a Professor in the Mechanical Engineering department at Stanford University. Dr. Kenny received his PhD in Physics from UC Berkeley.
Dr. Kenny's research group is researching fundamental issues and applications of micromechanical structures. These devices are usually fabricated from silicon wafers using integrated circuit fabrication tools. Using these techniques, the group builds sensitive accelerometers, infrared detectors, and force-sensing cantilevers. This research has many applications, including integrated packaging, inertial navigation, fundamental force measurements, experiments on bio-molecules, device cooling, bio-analytical instruments, and small robots. Because this research field is multidisciplinary in nature, work in this group is characterized by strong collaborations with other departments, as well as with local industry.
Need help? Get in touch
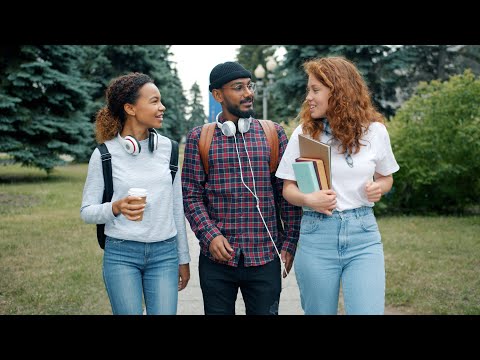
Pearson eTextbook: What’s on the inside just might surprise you
They say you can’t judge a book by its cover. It’s the same with your students. Meet each one right where they are with an engaging, interactive, personalized learning experience that goes beyond the textbook to fit any schedule, any budget, and any lifestyle.
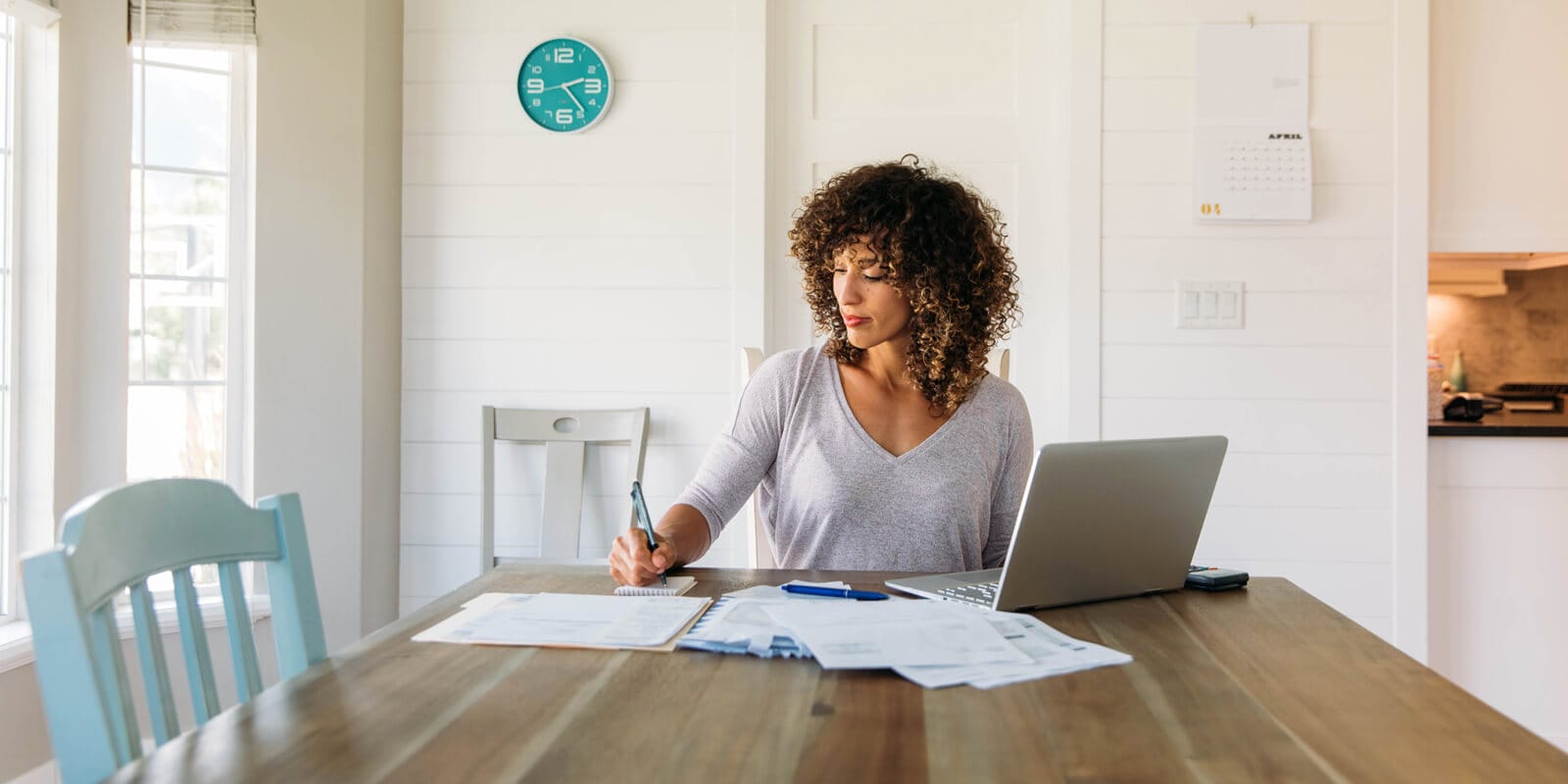
Digital Learning NOW
Extend your professional development and meet your students where they are with free weekly Digital Learning NOW webinars. Attend live, watch on-demand, or listen at your leisure to expand your teaching strategies. Earn digital professional development badges for attending a live session.